What Are Absolute Encoders and Incremental Encoders? Differences and Applications
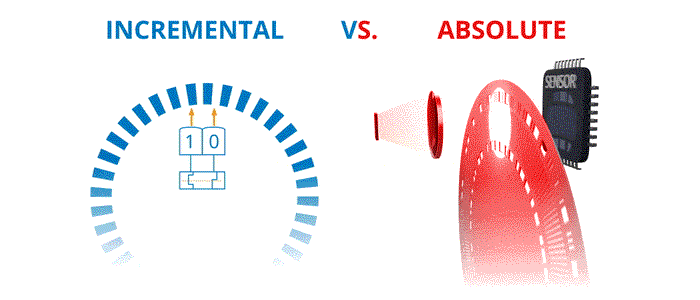
Encoders used in industrial automation systems precisely measure and control machine movements. The two most common encoder types, absolute encoders and incremental encoders, are designed to meet different needs. In this article, we will explore what these two encoder types are, their differences, and where they are used.
What is an Absolute Encoder?
An absolute encoder is a type of encoder that generates a unique signal for each position, retaining position information even in the event of a power outage.
- How Does It Work?
Absolute encoders transmit position information by reading encoded patterns on a rotating disk using optical, magnetic, or capacitive sensors. - Advantages:
- Provides an absolute value for each position.
- Unaffected by power outages.
- Offers high precision and reliability.
- Applications:
- Precise motion control in robotic systems.
- Hygienic and reliable measurements in the food and pharmaceutical industries.
- Position tracking in heavy industry applications where safety is critical.
What is an Incremental Encoder?
An incremental encoder is a type of encoder that measures movement relative to a reference point. It loses position information during a power outage but can be reset by establishing a reference point at the start.
- How Does It Work?
Movement is detected via incremental holes or lines on a rotating disk, generating a pulsed signal. - Advantages:
- Simpler and more cost-effective.
- Ideal for speed and direction measurement.
- Compact and easy to install.
- Applications:
- Motor speed control and feedback systems.
- Precision motion applications like CNC machines.
- Product flow monitoring in automation lines.
Differences Between Absolute Encoders and Incremental Encoders
Criterion | Absolute Encoder | Incremental Encoder |
Power Outage | Retains position information. | Loses position information. |
Precision | High (unique position data). | Requires a reference point. |
Purpose | Position tracking. | Speed and direction measurement. |
Cost | Higher. | More cost-effective. |
Installation | Complex. | Simpler. |
When Should Each Encoder Be Used?
- Situations Requiring Absolute Encoders:
- Systems demanding high precision and safety.
- Applications where power outages frequently occur, making position retention critical.
- Critical sectors like robotics, heavy industry, and food manufacturing.
- Situations Requiring Incremental Encoders:
- Applications focused on speed measurement and direction detection.
- Systems requiring lower complexity and cost.
- Industrial production lines and motor control systems.
Conclusion
Absolute and incremental encoders are powerful tools designed to meet different needs. Selecting the right encoder enhances system performance while optimizing costs. As the Turkey and Middle East distributor of TR Electronic, Üniversa offers a wide range of products tailored to your applications.
For more detailed information, contact us and find the most suitable encoder solution for your needs!