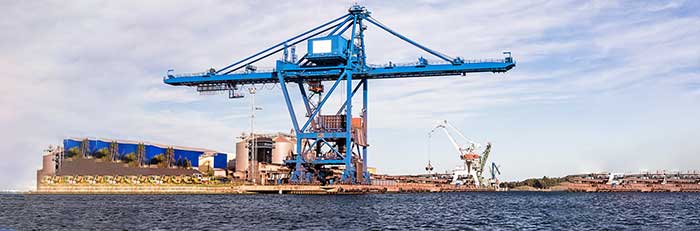
Port Machinery
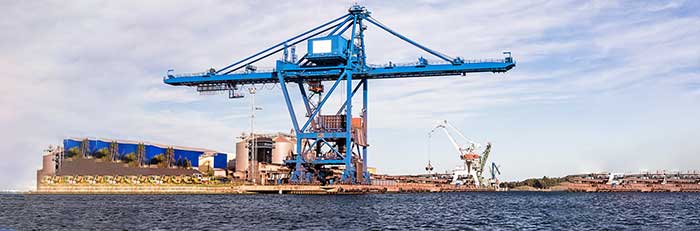
Port Machinery
Dock container cranes adopt multi-functional anti-tipping and anti-sagging technology, advanced hydraulic control technology. When the deflection machine hangs in the cabin, it automatically cuts off the power of the control system, instantly opens the hydraulic valve, and the cylinder is quickly emptied to avoid oil accidents. The container hanger prevents the crane and the cabin from being damaged. For TR linear displacement sensor, the stroke of the hydraulic cylinder is 1600 mm. Each hydraulic cylinder extends by 800 mm when the cylinder is operating in the minimum position. The 0mm~800mm stroke of the oil cylinder is used for cabin protection, and the remaining 800~1600mm stroke is used for the tilting movement of the spreader and the adjustment of the wire rope length. Features: anti-shock and anti-vibration; standard outer tube, compressive strength up to 700 bar; electronic components and waveguides can be easily replaced without pressure backing.
Existing solutions in automation applications of ports and lifting machines all need to use external modules to diagnose the status of the encoder and the safety of the output data. TR electronic specializes in encoder safety. Profisafe has released SIL 3 security certified encoders based on Open security and other security protocols. No additional security module is required. Data can be transmitted directly via PROFIsafe. It can only be used by completing the power and communication connections.
We offer CD_582 series, CD_75 series, CDV115 series and multiple safety encoders that comply with SIL3/PLe safety certification standards. The safety encoder ensures the functional safety of the position sensor. The use of certified standalone components enables the system builder to more easily enforce security requirements and stricter security guidelines.
Safe speed ensures that the motor does not overspeed or safely reach the required operating speed before starting a certain motion action.
Synchronous operation monitoring
The use of a safe absolute encoder (master system) and an encoder (slave) with additional safety functions can realize safe synchronous operation of different axes.
Axis status monitoring
By using a safety encoder (master system) and an encoder (slave system) with additional safety functions, overload condition or disturbance detection of the rotating shaft can be realized.